What is a CMMS?
- anniemurray
- Jan 26, 2021
- 4 min read
Updated: Jan 27, 2021
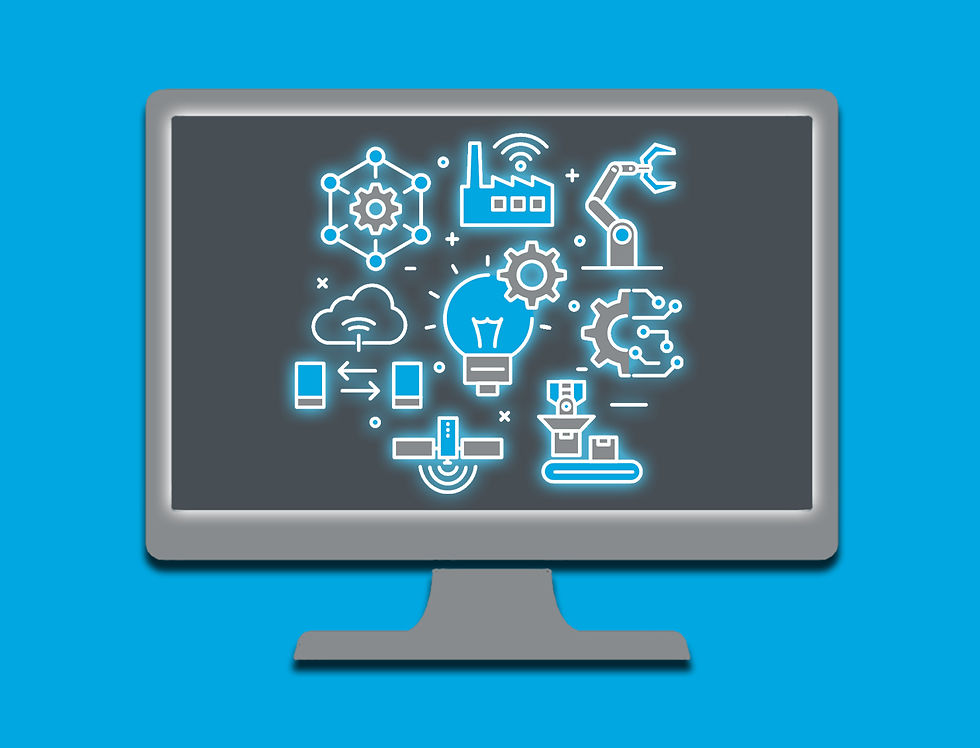
Plus 7 airtight reasons you need one!
If you work in maintenance and operations management, chances are that you’re either engineering-minded or good with your hands – or both. You understand machines. You might have a real knack for process. As a manager, you probably have a way with people, too. What you may not enjoy so much are the endless stacks of paperwork, the frustrating stream of equipment repairs, the logistical nightmares and the unpredictable bouts of downtime.
That’s where CMMS software comes in to make your life a heck of a lot easier. CMMS stands for computerized maintenance management system. Essentially, a CMMS is a big ol’ database that stores all of your maintenance data (like, all of it) and categorizes and organizes in a way that is useful to you for planning, budgeting and reporting and hopefully seamlessly integrating with your other operations systems. The result is one central resource that allows you to view and understand operating condition data in real time, trigger work orders and/or billing, and perform a wide-range of reporting tasks. There are tons of reasons why you should consider implementing a CMMS, but we’re going to go ahead and give you seven concrete ones right now. Take a look:
1. Faster workflows
Planning, scheduling, tracking, reporting, billing – the functions of your job take time. The most obvious CMMS perk is that by digitizing these processes, you no longer have to take time filling out paper copies for technicians, and they no longer have to fill out paper inspection forms that may end up sitting in a van or on a desk for days. Your CMMS also gives you a quick view of work order statuses, technician availability, cost concerns and more – all so that you can make quick, data-informed decisions on a daily basis. Depending on your integrations, you may also be able to trigger automated work orders, invoices and reports.
2. Improved maintenance tracking
A core function of the CMMS is providing automatic activity logs on every single piece of equipment you have – for the entire life cycle of each asset. So, what’s gone wrong before, what’s being worked on now and who’s completed the work. This knowledge keeps you in the know on current tasks, as well as enables you to calculate mean time between failure (MTBF), mean time to repair (MTTR) and other useful metrics. Which assets are costing you the most? Which employees are most productive? With instant access to this kind of data (and more!), your CMMS helps you track trends and troubleshoot in real time.
3. Clear asset health snapshots
This is where we need to geek out for a minute and tell you how really stinking cool a CMMS is. The platform can do a lot more than just collect and store data. If your CMMS integrates with IoT sensors and utilizes artificial intelligence, you can up your game with real-time, condition-based monitoring. You can set custom thresholds for your equipment, instantly prioritize maintenance based on health indicators, get quick-glance views into holistic condition data or drill down into individual assets. And, with color-coded charts and graphs, you no longer need to sift through rows of Excel data or file cabinets of paper. Your eyes will thank you!
4. Increased safety
All that awesome maintenance tracking can help you move from reactive, break/fix mode into preventive maintenance. This inherently results in more time spent on lower risk, planned tasks and less time on unplanned work on unstable equipment. Additionally, your CMMS can store all of your employee safety training records, making it way easier to stay on top of who needs to complete safety training or renew safety-related certifications.
5. Hassle-free compliance reporting
Ah, regulatory and insurance standards and audits - not to mention ISO 55000. Something we’re all familiar with… just like we’re familiar with the hours and hours it can take to compile the necessary compliance reports. Luckily, with a real-time activities log, your CMMS offers an easily accessible record of who did what and when. What’s more, it has the ability to sort by equipment types, facility locations and other attributes that may be needed for insurance or compliance reporting. Generating reports is a cinch, not to mention downloading and exporting them.
6. Streamlined communication
Your CMMS offers a secure, cloud-hosted central location for all your maintenance data. Most allow for multiple users and permission levels. This means you can communicate with your team remotely and technicians can access real-time data from the field. Do you need to change the priority of a task? Have a specific comment about a finicky piece of equipment? Want to attach a photo? With custom work order functions and push notifications, your CMMS ensures that your crew stays up-to-date on all assigned tasks. All that super specific equipment and work order data at your fingertips also comes in handy when onboarding new employees.
7. Increased productivity (and profit!)
All of the benefits we’ve outlined so far really add up to one big one – productivity. With a CMMS, you can ensure you have the right people working on the right equipment at the right time. This level of precision creates efficiencies you’ll see in your labor costs, inventory management, customer service and, ultimately, your bottom line. With safer, more reliable equipment, you can minimize costly downtime and get more work done – faster.
A CMMS isn’t the future of maintenance management. It’s the best practice for right now and a solution that can grow with your business as needs change. Interested in learning more? Get in touch any time!
Comments